The Process Of Custom Metal Fabrication
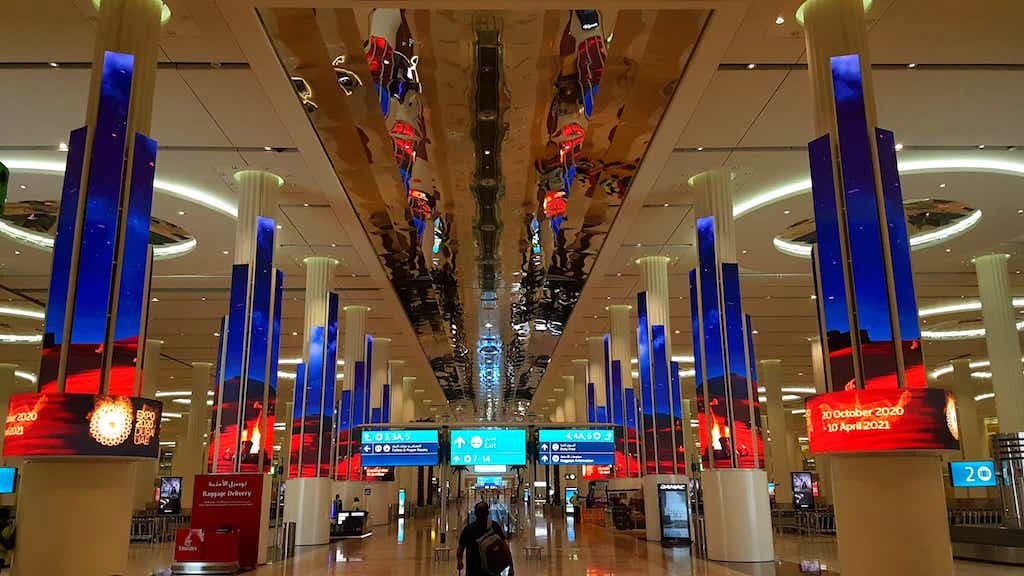
Custom metal fabrication is a multi-step process that changes raw metal into specialized components tailored to meet specific needs. This process involves cutting, bending, welding, and assembling metals like steel, aluminium, and copper into finished products. Each stage requires precision, expertise, and specialized equipment to ensure the final product meets the exact specifications of the project. Here, we will break down the custom metal fabrication near me process to understand how it works from start to finish.
Design and planning:
The first stage of custom metal fabrication begins with design and planning. The project starts with a detailed blueprint or a computer-aided design (CAD) model, which outlines the dimensions, shapes, and specifications of the metal component. This step is important as it allows the fabricators to visualize the final product and identify any challenges before production begins. Engineers and designers collaborate to ensure the design is practical, achievable, and meets the required tolerances.
Tools used: CAD software, 3D modelling.
Cutting the metal:
Once the design is finalized, the fabrication process moves to cutting. In this stage, raw metal sheets, bars, or tubes are cut into specific sizes and shapes. There are several cutting techniques used depending on the material and complexity of the design. Common methods include:
- Laser cutting: Ideal for precision cuts, especially on complex shapes and designs.
- Plasma cutting: Used for thicker metals, offering clean and quick cuts.
- Water jet cutting: Utilizes a high-pressure stream of water to cut metal without generating heat, preserving the material’s integrity.
Tools used: Laser cutters, plasma cutters, water jet machines.
Bending and forming:
After the metal is cut, the next step is bending and forming it into the desired shape. This is done using machines like press brakes that apply pressure to the metal to bend it at specific angles. The bending process must be highly accurate, as incorrect angles can result in misaligned components.
Tools used: Press brakes, rolling machines, bending machines.
Welding and assembly:
Once the individual metal components are cut and shaped, they are welded together to create the final product. Welding is a key part of metal fabrication, as it joins different parts and ensures structural integrity. Different welding techniques, such as MIG, TIG, or arc welding, are used depending on the type of metal and the strength required. After welding, any necessary assembly of the product occurs, with additional components being added if required.
Tools used: Welding machines, clamps, fixtures.